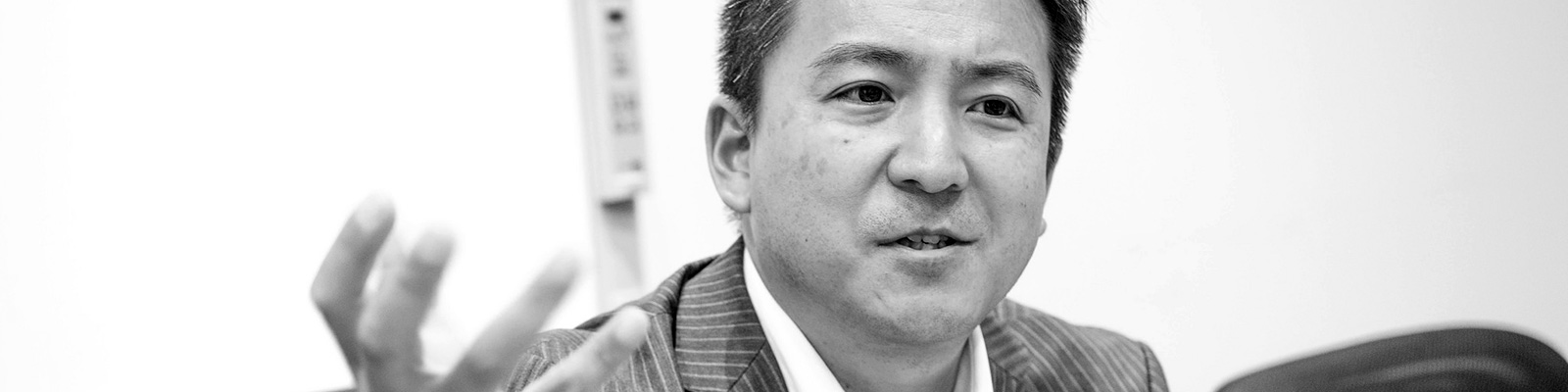
シスコシステムズ シスココンサルティングサービス 八子知礼氏(前編):かつての「最新」に縛られて身動きがとれない日本の現場
日本のIoTを変える99人【File.003】
2015.10.15
Updated by 特集:日本のIoTを変える99人 on October 15, 2015, 06:30 am JST
日本のIoTを変える99人【File.003】
2015.10.15
Updated by 特集:日本のIoTを変える99人 on October 15, 2015, 06:30 am JST
IoTといえばドイツのIndustrie 4.0が引き合いに出されるように、製造業の現場を大きく変えつつある。だが、かつて先端をいっていた日本の製造業は、それにこだわりすぎるがゆえに現在遅れをとっている企業もあるという。この状況を憂慮し、業界内外に向けて情報発信・啓蒙活動を続けているのが、シスコシステムズ合同会社 シスコ コンサルティング サービス部門でIoT/IoEコンサルテーションを手掛ける八子知礼氏だ。日本の産業界の現在の問題点と、これからどうすべきかについて、八子氏に語っていただいた。
私は2010年頃から「モバイルクラウド」という概念を提唱してきましたが、人がモバイルでクラウドにつながるようになったら、次はモノがつながるようになり、やがては機械と機械が通信する、当時の言葉でいえばM2Mのビジネスが大きくなると予測していました。もともとクラウドとは親和性が高いM2Mが、IoTと呼ばれるようになり、ようやく立ち上がってきたかなと思っています。
M2MがIoTと呼ばれるようになったのは、2014年にGEが中心になって「Industrial Internet Consortium」(IIC)を結成したところからでしょう。それ以前にも製造業にはドイツを中心にしたIndustrie 4.0の動きはありましたが、2012年の時点ではまだ火がついていなかったと個人的には解釈しています。ここまで爆発的にIoTが広がったのは製造業、中でもGEが起爆剤だったと言っても過言ではないでしょう。今や、あまりIoTとは言えないようなものまでIoTという言葉がつくようになったのも黎明期のクラウドビジネスと同じかもしれません。
そして今、その動きに、日本は取り残されかけています。
IoTは、いろいろなものにセンサーをつけることで、「人間ができないことを補ったり、きめ細かいサービスをする」という発想が一番簡単なものですが、それはもともと日本が一番得意だったはずのことです。工場のスマート化や自動化も、お家芸と言ってもいいぐらい日本の工場はかれこれ20年、いやもっと前から先進的にやってきたはずです。
ですので今、製造業の方にIoTの話をしても「既にうちははるか前から取り組んでいます、これ以上やることはありますか」と言われます。しかし自信を持って言いながらも「ドイツやアメリカの取り組みとはちょっと違うみたいだなあ」と内心思っていらっしゃるようなんです。それでも自負はあるので「うちの工場は最新、最先端です」とおっしゃることに数多く出くわします。
といっても、それは15年前にやりきったとか、良くても5年前にできた工場だ、という話ばかりです。その頃はモバイルもクラウドも現場でフルに活用できるソリューションではありませんでした。分析可能なコンピューティング環境があっても、取得したデータをリアルタイムで分析することまではできていなかったでしょうし、今の様なすさまじい量のビッグデータではなかったはずです。さらに自動化や機械と機械の連携まではできていても、連携して動作した結果が本当に後工程や社外まで含めて全体最適化されていたのかどうかまでは検証、反芻できていないと思います。すなわち、この5年でできることが激変しているだけでなく、把握・分析しなければならない範囲やデータの量が爆発的に増えているわけです。それが勘案されていないのに「既に取り組んだ」と言われるケースが多く存在します。
例えば、とある工場では、オペレーションが順調な時にはFA(Factory Automation)でフルに自動化されて無人のラインなのに、何かの原因で止まった瞬間に、鉛筆とノートを持った方々がラインに出ていく風景が散見されました。ついさっきまでコンソールルームでFAの画面を見ていたはずなのに、その画面をタブレットで持ち出すという発想がないか、そのニーズはここ3年ほどで盛り上がってきているのに、FAベンダーに見積依頼すると驚く様な金額が返ってきてあきらめているかなどです。私から見れば、実は繋がっているようでFAと人が“つながっていない”ことにものすごく違和感があります。結局現場は勘と経験で動いているという状況は改善されていないので、自動化されてスムーズに動くようになったのは平常時だけで、エラーが発生するととたんに昔に戻ってしまいます。
「トラブルが発生したら小さい環境をラボで検証、再現してみる」といったことも生産技術検討部門の方々はおっしゃいます。かつてはそうしなければ改善できなかったかも知れませんが、今なら本番環境のセンサーで集めてその場でリアルタイムに分析し、未然にトラブルが発生しないよう防止することに取り組むこともできるのです。かつて進んでいただけで、ここ5年のすさまじいテクノロジーの恩恵を取り込み切れていません。これは前述のようにFA企業にも問題があったかも知れませんし、IT企業が現場に入り込まずに提案を逃げてきたことも一因でしょう。たしかに自動化は高度に実現できてはいますが、捉えきれないほどの大量の稼働データをリアルタイムにとらえて分析し、結果を現場にフィードバックするということができていないのです。
分析結果のフィードバックを嫌がる現場の体質も問題です。小売店の店頭や労働集約型の飲食店などは特にそうです。「忙しくてデータを見る暇がない」「きれいなレポート見てもそれで何をしろと言うんだ」と言い訳して、分析結果を使わない。売れ筋がデータで明らかになっていても、それを使わず人の勘と経験に依存する。そんなことをしていて徐々に労働人口が減ってゆくのに、生産性を上げていかなくていいんですかと言いたいです。もちろん、きれいな分析結果を投げつけて終わっている管理部門やIT部門にも問題があって、現場の作業負荷を軽減したり、実行可能なアクションを指示するまでには甚だ至っていません。
欧米の最先端の工場では、「人の判断」ができるだけ業務の中に入り込まないようにプロセスを組み立てます。以前は工場の生産ラインを徹底的に自動化しても、それを司る最終的な需給予測や生産計画といった領域に関しては「意思入れ」と言って、営業や経営からの要請などによる人の意思決定で“調整”せざるを得ない事が多々ありましたが、今はさすがにそんなことはしません。高度な予測と自動化が可能になればそれは必要ないからです。もちろん、日本でも多くの製造業や物流業でも同様な自動化に取り組んでいる例はありますが、さらに一つ一つの需要側からのニーズに自動対応するようなところまでは中々至っていないのではないでしょうか。
ドイツのIndustrie 4.0は、言い換えれば、マスカスタマイゼーションをすべての製造業に適用するという発想です。自動車業界では、生産する時ハンドル、シート、フロアカーペット、インパネの色をオーダーに合わせて変えて納車するようなことは広く行われていますが、同じことが他の業種でも広範に適用できるかといったら、今の日本ではまだ難しいのではないでしょうか。出来る技術は整ってきているのですが、そのニーズを広い切れていないので、ニーズがより個々人に割れてきた時代を想定して目指すべきレベルを定義しないと、いくら「進んでいる」と言っても、追いつかれて追い越されてしまう可能性が否めないことが私の懸念です。
アメリカではGEが中心となって推進しているIndustrial Internetでは、GEのみならず賛同する企業が自社に集まったデータをデータレイクという巨大なデータプールに放り込んで共有するのみならず、GEソフトウェアが作ったデータ分析・活用・流通プラットフォームを使って積極的にデータ活用しています。データの販売や流通も始まっています。かたや日本では、プラットフォームは自社のノウハウだから絶対に外には出さない、データもなぜ売るんだと考えてしまいます。売れるものは何でも売る、プラットフォームになれば簡単に切られることはなくビジネスを継続できる、そういうプラットフォーム志向が日本の製造や流通小売にはあまりないか、極めて消極的に見えます。フロントエンドで最先端を走り続けて疲弊するばかりで、成長エンジンを提供して儲けようという発想がないのです。経産省ではデータ駆動型イノベーション創出戦略協議会などでも議論がすすんできていますが、そのようなプラットフォーマーの育成が課題だと言われていたりします。
特筆すべきよい特性なのですが、日本はきめ細やかな感性を持ち、自分で自社で全部やりたがる、そしてそれなりにやれていまうという器用な国民性がそうさせるのでしょう。他の会社の方が良いものを持っていても全部自社で賄おうとします。テラスカイのジェイソン ダニエルソン氏(厚切りジェイソン氏)が登壇したパネル対談のモデレータをしたとき(ログミーによる書き起こし)に、彼も同じことを言っていました。外国人は競争力があって「すごい」と思うものがあればそれを採用して、周囲をそれに合わせて組み上げようとします。そもそも競争力があってすごいこと・ものに対して自分で類似のこと・ものを全部作るという発想がない。でも、日本人はすごいと思ったものがあればそれをまねて自分で器用に作ってしまうので、そのための投資コストがかかり、市場参入が遅れるので、投資が回収できない、そんなことを彼は鋭く切り取って語っていました。
日本の技術者は探求心が旺盛で優秀なので、まねて作ったものでも最終的な完成品は総じて安く他国で作るよりも圧倒的に品質が良いものができてしまいます。それは決して悪いことではありません。でも、「安い」というのは工場出荷時やサービスリリース時の卸値・原価が安いだけであって、開発にかかるコスト、投資が考慮されていなかったりします。ですので、モノやサービスはリリースされますが、市場のトレンドからは遅れて出てくるので回収が難しく、プロダクトやサービスが短命に終わってしまうことも多いですよね。それは技術者ではなく事業責任者の問題です。
工場の話に戻りますが、日本の最新鋭の工場だといっても、建造されたのは2010年頃、新しくてもせいぜい2012年頃です。もっといえば、工場の建設計画は稼働の2年ぐらい前から立てているので、提案されるのはその時点の技術レベルのもの。つまり2010年稼働の最新鋭の工場であれば、2008年のトレンドだった技術でできています。繰り返しになりますが、2008年といえば、モバイルもクラウドもまだなかったし、ソーシャルメディアをビジネスで活用するなんて発想もなかったし、まして工場のすべての機械にセンサーを取り付けて全てのデータをキャプチャして機械学習で分析なんて、そんな夢見たいこと言うなと言われる時代です。当然、今となっては古くなっている部分も多いですが、全部すり合わせ技術で作っているため、古くなっている部分だけを入れ替える際には莫大な追加投資が必要になるため、容易に入れ替えることができないわけです。
そうならないためには、「インフラ」「プラットフォーム」「フロントエンド」のレイヤーに分けて、別々に入れ替えができるようにすることが一例として考えられますね。インフラは長く使う、フロントエンドはその時最新のものを使う、プラットフォームはその中間、と分けて考えます。それぞれがモジュール化されており、複雑に相互依存するのではなく疎結合であることが重要です。2013年頃から、プラットフォーム志向の工場が増えてきています。
車づくりの発想と同じで、日本車はどちらかといえばすり合わせ技術で作っていますが、海外メーカーの車はマフラーが壊れただけでもパイプまで含めたモジュールを全部交換したりします。モジュール化することで修理やメンテナンスにコストがかかりますが、その分他モデルへの使いまわしによるコストダウンや新モデルの開発スピードアップに貢献しています。これと同様の発想で製造業のみならず小売や流通、社会インフラなどの現場部門でモジュール化、プラットフォーム化が重要な考え方になってきています。
(後編に続く)
構成:板垣朝子
IoTは我々の暮らし、仕事、産業をどう変えるのか。またどのような技術やソリューションが生み出されているのか。これから乗り越えるべき課題は何なのか。さまざまな視点から、日本が目指すIoT社会の姿と今後の変革について、日本のIoTのをリードするエバンジェリスト、企業、チャレンジャーの方々に語っていただく連載企画です。